[Technical x]
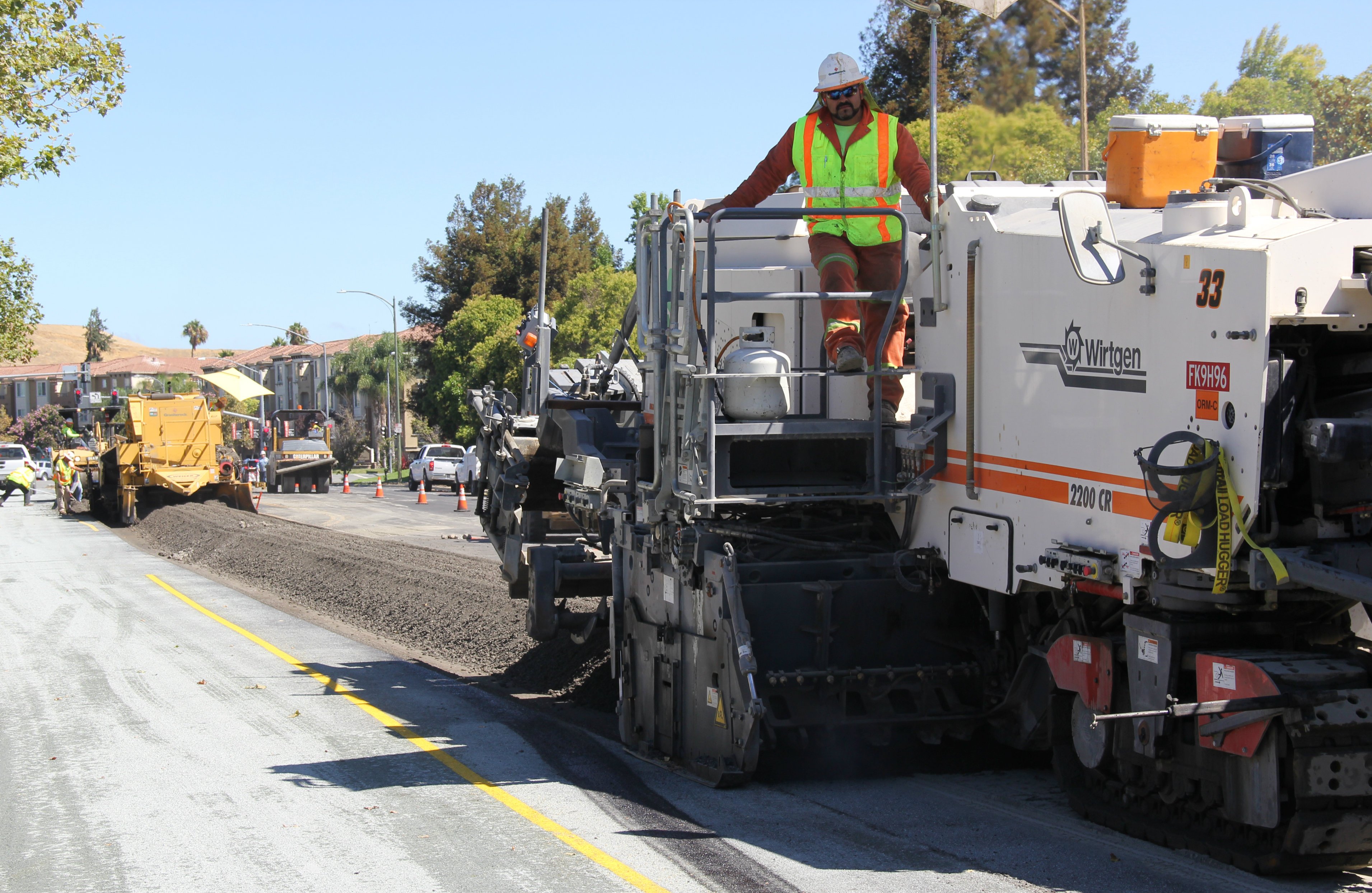
Five reasons your roads need Partial Depth Reclamation
Posted by Shanna Crigger on Sep 21, 2015
As California faces a growing crisis of crumbling roadways, it turns out there is a way to tackle our aging, broken up streets without going broke or sending another bond measure to the voters.
Read More
Read More
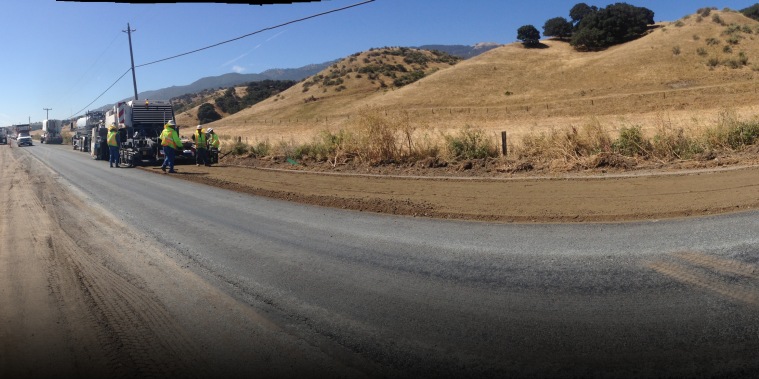
PDR team covers record ground on River Road project
Posted by Shanna Crigger on Jul 15, 2015
A recent partial depth reclamation (PDR) project on River Road near Chualar exceeded expectations on several fronts.
Read More
Read More
Paving Highway 152: New leadership on the night crew
Posted by Shanna Crigger on Jul 2, 2015
On the outskirts of Gilroy, Graniterock’s Construction team is grinding and paving a 12-mile stretch of Highway 152.
Read More
Read More
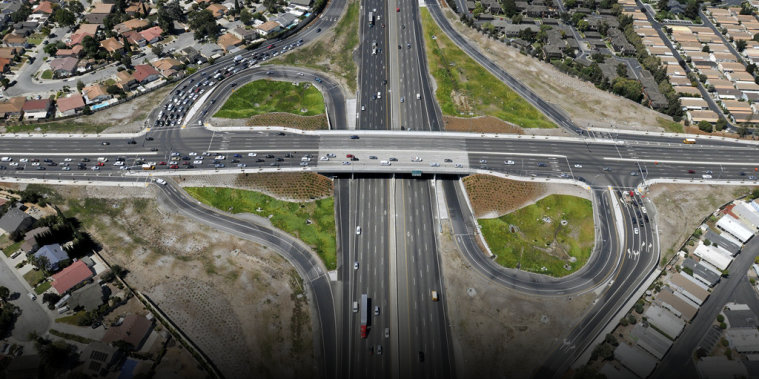
Capitol Expressway interchange wins project of the year from APWA
Posted by Shanna Crigger on Jun 4, 2015
Graniterock’s Capitol Expressway to Yerba Buena Interchange job won 2015 Project of the Year from the APWA Silicon Valley Chapter in the Transportation $5-$25 million category.
Read More
Read More
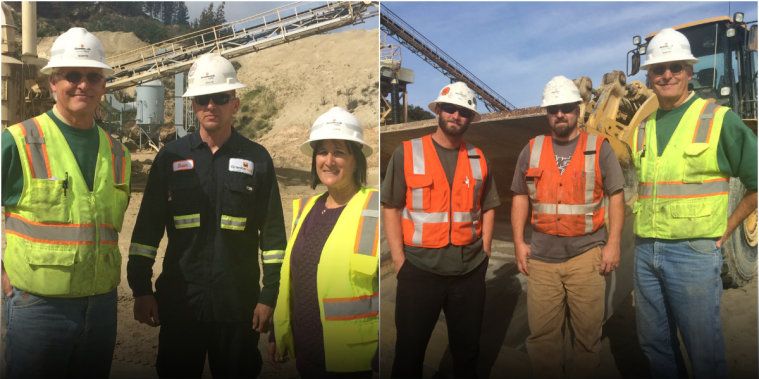
Working Together: Small team keeps sand plants running smoothly
Posted by Shanna Crigger on Apr 17, 2015
Marvin Brandt didn’t know a single thing about sand before taking over the Santa Cruz and Quail Hollow sand plants seven years ago. But what he knew, and knew well, was how to manufacture materials and lead people from nearly 30 years as production manager at Cemex, just a few miles up Highway 1 from the Santa Cruz Sand Plant. “The principles of manufacturing are the same whether it’s sand or cement,” said Marvin, who splits his time between the Santa Cruz and Felton plants. “Success comes from the people you’re working with, and I’ve got the best crews.” Marvin inherited two struggling sand plants when coming on board to Graniterock in 2008. Both plants were in need of equipment upgrades and had difficulty meeting customers’ expectations. To make the job even more challenging, the Santa Cruz plant is going into its second year without a mining permit extension from the U.S. Department of Fish and Wildlife, which has limited production in Santa Cruz and forced Quail Hollow to double its sand production to help the Santa Cruz plant meet customer demand. Through the daily challenges and permit uncertainty, Marvin and his small team – Ben Snowand Neil Kunkel in Santa Cruz, and Cynthia Escobar, Enrique Diaz and Shaun Eskue at Quail Hollow - maintain calm and order. They ensure stockpiles are kept up, plant machinery stays in working order and customers are loaded with the right quality and quantity of material. Sand specs are extremely tight, which means the team is constantly fine tuning production to make sure the material is neither too fine or too course. Golf courses, in need of bunker sand, are typically the plants’ top customers. While Marvin is quick to credit his team for the plants’ turnaround, the team is equally quick to praise their leader. “Marvin’s a good teacher,” said Ben, who has worked at the Santa Cruz plant for three years. “He makes you want to come to work here and do a good job.” Neil said he enjoys Marvin’s easy going personality and works hard to earn the trust Marvin has in everyone. “He trusts us to do our job and he makes it so you enjoy coming to work,” Neil said. “Anything we need, he’s happy to help.” Cynthia, weighmaster at Quail Hollow, worked with Marvin during her 18-year career at Cemex before joining Graniterock in 2011. Because the Quail Hollow team is small, they treat each other like family, which is due largely to the culture Marvin has helped build. “We get to know each other on a personal basis and take interest in each other,” Cynthia said. “Marvin’s a good listener. He’ll listen to each one of us before making any sort of decision, which is really nice.” For Marvin, leading a team and taking responsibility for two major production facilities is akin to parenting. He and his wife of 39 years know something about that with three sons and four grandchildren. “You work alongside them. They see how you operate, how you work,” he said. “You can’t tell someone I want quality, safety and production. You have to show them how it’s done. “It’s like raising a child. Children learn what is right by watching.”
Read More
Read More
Making SFO Safer: Graniterock Completes Installation of Engineered Materials Arrestor System (EMAS)
Posted by Rose Ann Woolpert on Mar 18, 2015
For three months this summer, the pounding of compactors, shrill of back up alarms and reverberation of rollers and excavation equipment competed with the roar of jets taking off and landing at San Francisco International Airport. Graniterock Team Members and joint venture partner DeSilva Gates Construction were busy installing new Engineered Materials Arrestor System (EMAS) safety devices on two of the airport’s four major runways.
Read More
Read More
Major Changes in Hot Mix Asphalt: Caltrans Adds More "Superpave" Concepts to Improve Performance
Posted by Mike Cook on Mar 18, 2015
In recent years the California Hot Mix Asphalt (HMA) industry has seen major changes in technology and state specifications. Warm mix asphalt, recycled asphalt pavement and anti-stripping agents have already been implemented, and the use of intelligent compaction and asphalt shingles are hitting the street soon. Further changes in specifications include a new binder grading system (PG grades), a shift in responsibility for quality control from owner to contractor (QC/QA) and tighter tolerances for materials used in HMA Caltrans Section 39.
Read More
Read More
A Good RAP: Reclaimed Asphalt Pavement
Posted by Mike Cook on Mar 18, 2015
Reclaimed Asphalt Pavement (RAP) can be used as an aggregate and partial oil replacement in the hot recycling of asphalt paving mixtures. The most common method (conventional recycled hot mix) involves a process in which RAP is combined with virgin aggregate and new asphalt cement in a central mixing plant to produce new hot mix paving mixtures.
Read More
Read More
What Makes Concrete Green?
Posted by Katha Redmon on Mar 18, 2015
An important part of the design phase of any construction project is materials selection. Concrete, steel or wood are typical options for the building frame; for paving applications, the choice is generally either concrete or asphalt. Material choice depends on several factors, including initial cost, life cycle cost and performance for the specific application. Due to the growing interest in sustainable development, engineers and architects are now motivated more than ever to choose sustainable materials.
Read More
Read More
Concrete Aggregate - Not Just Any Old Rock
Posted by James Schmitt on Mar 18, 2015
By James W. Schmitt, Principal and President of Schmitt Technical Services: http://schmitttechnicalservices.com
Read More
Read More